Light-weighting Solutions to Make Car Suspension Systems More Compact: Materials-Focused
Friedhelm provides invaluable insights into the use of alternative materials, such as elastomers and composites, and the integration of aluminium in suspension systems.
Add bookmark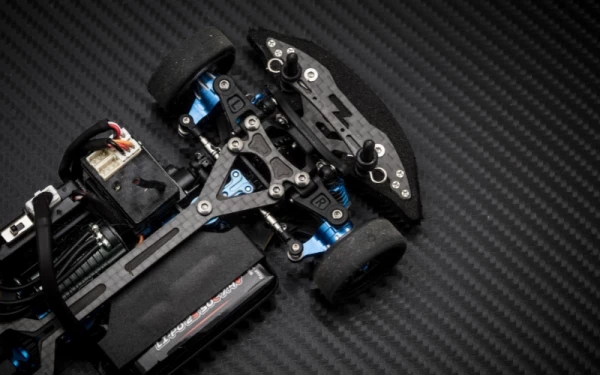
Light-weighting Solutions to Make Car Suspension Systems More Compact: Materials-Focused
In this exclusive interview between Automotive IQ and Friedhelm Nattland, Director of Engineering at Hendrickson Europe, Friedhelm gives his knowledge on the innovative approaches and cutting-edge technologies driving the evolution of suspension systems towards greater efficiency and reduced weight.
Friedhelm provides invaluable insights into the use of alternative materials, such as elastomers and composites, and the integration of aluminium in suspension systems. He also addresses the challenges and considerations associated with these advancements, shedding light on the pivotal role of recycling in achieving sustainable, lightweight solutions.
Q: What alternative solutions can be made to make suspension systems and components lighter?
Friedhelm
Besides our principle of ‘design to weight optimum’ we at Hendrickson are using alternative materials for core elements of a suspension. For instance, replacing steel leaf springs with elastomer springs or composite leaf springs. The same is valid when we use aluminium for the structural components of the suspension. These materials have substantially better function-weight ratios than steel springs or steel castings.
Q: One of the topics you'll cover at the conference is the viability of using aluminium in suspension systems for low/mid-range vehicles. Could you share some insights on the advantages and potential challenges associated with this approach?
Friedhelm
Designing and producing suspension components from aluminium have a relevant weight advantage compared to steel fabrications or castings, a further advantage is limited corrosion. Reusing or recycling is comparable to steel-based parts; because of the lower tensile strength of aluminium compared to steel, aluminium parts need increased wall thickness or mounting footprint to component interfaces.
This can cause challenges in the packaging space. Furthermore, the total part costs are higher which may not leverage the weight advantage. Every application needs an individual business case review.
Q: Could you shed light on whether recycled materials are a viable solution for achieving lightweight suspension systems, and how/why?
Friedhelm
The requests for a circular economy are constantly increasing to comply with the routes to sustainability set out in European community plans. For steel and aluminium components, recycling is already implemented in mature industrial processes. Our natural rubber-based elastomer springs can be recycled into rubber pellets and be used as valuable filler for pavements, for instance. A re-vulcanisation process to substitute virgin rubber in polymer raw material is under development, and with encouraging results so far. Recycling of composite springs into valuable raw materials is under development as well. Perspectives are to use the composite after pre-treatment processes in cement kilns or as filling granulate in thermoplastic components.
Q: How can composite materials, including glass fibres and resin, be an effective solution in weight reduction for trucks?
Friedhelm
Due to a deeply developed perfect mix of glass fibres and resin, the structural and flexural performance of composite components has an excellent function-weight ratio. This leads to a weight reduction of 30%, all the way up to 60% of specific components compared to steel-based products. Higher component costs of composite parts can easily be outweighed by higher income from increased loads and less fuel consumption on commercial vehicles.
Q: When introducing new materials to reduce weight, what are the potential challenges or concerns that may arise?
Friedhelm
One challenge is that components usually need to be completely redesigned and may include a costly validation process. If customers are not informed in detail of the new materials in the components a concern may arise from the customers whether or not the new components are durable for application under the rough usage conditions by trucks, for example.
Q: Likewise, what are some of the potential issues or considerations when using new composite materials and light alloys in suspension systems? Are there specific factors that engineers and manufacturers should be mindful of?
Friedhelm
As mentioned, components made from composite materials may need to be redesigned, and different production processes and potentially adapted assembling procedures must be tested for their durability, function performance and recycling. This typically impacts the modules; they are used in ways which may need re-designed as well. For instance, elastomer suspensions are completely different in design which needs a complete system design review if replacing a steel leaf suspension. In many cases, this effort is leveraged by the advantages of reduced weight.
Q: As the Director of Engineering at Hendrickson Europe, can you give us an overview of how your company is contributing to the development and implementation of light-weighting solutions in suspension systems? Are there any notable projects or innovations you'd like to highlight?
Friedhelm
Hendrickson is a technology leader in suspension system development, manufactures, and supplies to the global commercial vehicle market. We have developed benchmark products in lightweight and ride performance as suspension systems, integrated axles, trailer axles and components and we supply them to the market. Hendrickson is the global market leader for LITEFLEX composite leaf springs and ULTIMAAX and HAULMAAX elastomer heavy-duty suspensions. Our fabricated hollow steer axle STEERTEK has best-in-class function weights and contributes significantly to implementing lightweighting solutions into the market.