Polycarbonate Glazing is Clearly on Its Way: look through and find out why in this 2 part series
Add bookmark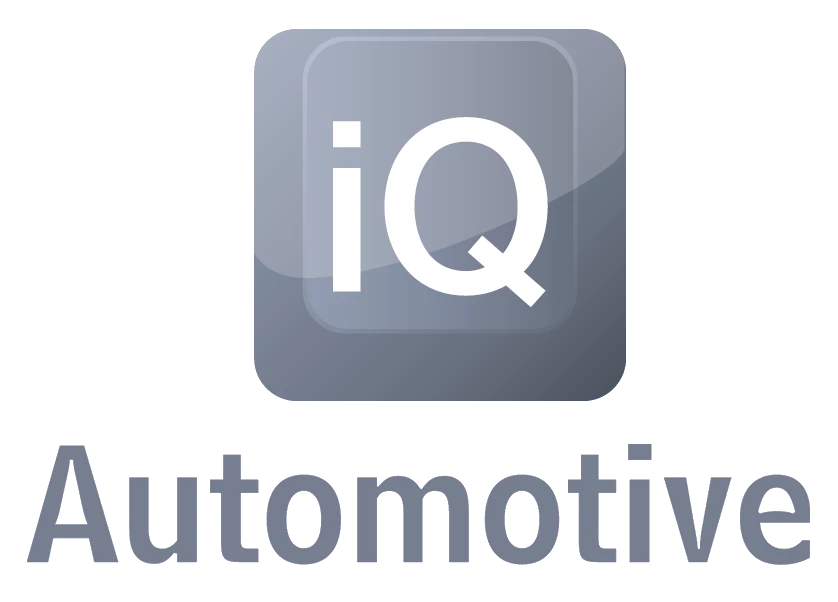
Automotive IQ editor Will Hornick interviewed Dr. Frank Buckel of Bayer Material Sciences. Dr. Buckel is the Director of Automotive Glazing & Sustainability and is a part of the UNECE |GRSG Informal Group on Plastic Glazing. This is part 1 of a 2 part interview series.
"The underlying basis of the existing regulation is relatively old and comes from
a time when no one considered having a glazing material other than glass.
Most of the tests are not so much concerned with what is needed but more
with what glass can deliver."
Automotive IQ: What is your background and your role at Bayer Material Science?
Frank Buckel: I studied chemistry at the University of Stuttgart and got my PhD in organic chemistry. Then I started at Bayer in 2000 in central research and transferred later to the business unit, Polycarbonates. Polycarbonate is one of the polymers that Bayer is producing and selling. I’m in the Innovation Department. We are doing developments in the field of polycarbonate and it´s blends and it´s applications, from CD/DVDs to electronic components up to automotive products. For example, the headlamp covers are made of this material and, of course, we are also developing materials for the glazing market.
Automotive IQ: What are the current uses for polycarbonate in the vehicle and how do you think that might change in the next three to five years?
F.B.: One example I already mentioned is the headlamp covers. Due to the fact that you can injection mold polycarbonate, you can, of course, use it as styling element integrated in the car body. In recent years, the front of the car has changed and the headlamp covers have become the eyes of a car. You also have some outdoor parts that are mainly polycarbonate blends and also PC films and PC blends for the interiors. It’s already a good and interesting application area for us but, of course, the largest potential not yet really opened up is in glazing.
Automotive IQ: I understand that there have been some innovations with regard to coatings particularly in abrasion resistance. Do you think you could highlight some of those innovations and how they might influence the market in the coming few years?
F.B.: If you want to enter a typical glass application with polycarbonate you definitely need some surface protection due to the fact that the abrasion resistance and the weathering are not as good as glass. You need a coating on top of the polycarbonate whose main function is protection. Protection against UV light and protection against scratches and there has been a lot of R&D on this topic and nowadays we have much better coatings available for these applications than in the past. The first applications were back in 1989 for a small side window of the Smart car. That was behind the driver and no one was really using this window for looking at the street or following the traffic so the coating was tailored to this kind of application. The abrasion resistance was good enough for that. But that changes if you go to other glazing locations and their requirements are definitely higher. So the performance increase in coatings achieved until now is key to broaden the use of plastic glazing since the requirements for different glazing locations are not the same. For example, in the roof area, which is already an existing application, the abrasion resistance isn’t that important. I won’t say, it is not important but, from a regulation standpoint it’s not important at all. Abrasion on the roof is not tested there but, of course, regulation is one point and the quality aspects the car manufacturers want to achieve are another. So you don’t need the same abrasion performance for a roof as for a windscreen. That’s on its way.
Automotive IQ: You mentioned regulations. I understand that Regulation 43 is what currently governs the testing of automotive glazing. But the regulation dates back to the early 1980s. In your opinion, how could an updated regulation more effectively govern modern glazing materials? Obviously, keeping safety in mind.
F.B.: That’s true. The underlying basis of the existing regulation is relatively old and comes from a time when no one considered having a glazing material other than glass. Most of the tests are not so much concerned with what is needed but more with what glass can deliver. Of course, a glazing material that does not break in case of an accident would be fine, but if your only choice is glass - a hard and brittle material - that won’t happen. So you concentrate on a safety level that can be delivered by the only - at that time - available material which is one-layer safety glass leading to small pieces of glass in case of breakage. And laminated glass where the pieces of glass adhere to the inner layer film in case of breakage. Then transparent plastic came up and was also considered for that application but still the tests that are needed and the regulations are more or less based on historical decisions about what glass can deliver. It’s a problem in some cases; you need different kinds of tests. No one, for example, would test normal glass for weathering. But, laminated glass with a film inner layer is tested against UV radiation so this kind of test exists already. And for plastics you need again a different weathering test, a so-called artificial or accelerated weathering test. So the problem is more that you cannot exactly copy and paste the existing tests because the benefits and disadvantages of the tested materials are a little bit different.
So if you want to assess safety, you have to do different tests and the other problem is, of course, at the beginning no one said we want to have this material as a windscreen; let’s start to allow it for some other areas. That’s the point we have at the moment, for example, in R43. There are no considerations for windscreens to be made out of plastic and that was the starting point for the informal group on plastic glazing with the job of defining tests that would make the use of plastic in windscreens safe. The second task was to review the existing tests to see if they are really suitable for plastics. So, that was the start of this group. The driving force at that point was police cars in Germany being fitted with plastic windscreens due to the fact that they are highly impact resistant. There are existing allowances for police cars to use plastic in all glazing parts, just to be safe if they were attacked by vandals or rioters. That was the reason for this. It has worked fine for years but the problem is that it is a special allowance only for the police. For example, there are also uses for polycarbonate windscreens in forestry machines. These harvester machines where they also consider high levels of safety in order to ensure that if parts of the trees hit the windscreen then the driver is safe behind it. There are existing applications which need greater protection and that was also the starting point where we said, well, obviously it’s possible, there are some safety advantages, why not consider testing it for normal vehicles?
Automotive IQ: Do you have the goal of updating the regulation or of replacing it entirely with a new piece of legislation?
F.B.: No, it will be an additional annex in R43. At the moment we have annex 14 which is called Rigid Plastic Glazings Other Than Windscreens. The idea is to have an additional annex called Rigid Plastic Windscreens or similar.
Automotive IQ: Currently legislation exists for the other windows in the car but not for windscreens, the most critical piece?
F.B.: Yes, windscreens made out of plastics are currently not allowed.
Automotive IQ: In your opinion, what needs to happen to reduce the cost of polycarbonate to make it competitive to glass?
F.B.: Probably one point, which should always be mentioned, is design. You can have a different design which you cannot make out of glass. So, for example, you can then avoid additional components that you normally need to assemble. In the first plastic glazing application in the Smart, there was a small spoiler integrated into the glazing part. That was the reason for the decision to use polycarbonate because if glass was used an additional frame would have been needed which then has this kind of spoiler or you had to change the design. That’s one area you can save money with reduced assembly costs. For example, on a roof, if you make the roof out of polycarbonate, you can already integrate by injection molding some guiding profiles e.g. for the sunshade.
Automotive IQ: So they become part of the structure?
F.B.: Yes. You don’t need to fix an additional guiding profile to the glass roof for a sunshade, for example. That's the crux; you have to discuss the whole situation in order to see where you can reduce assembly costs. Glass as a material, if you just compare flat square meters instead of complete glazing parts, if it’s one-layered safety glass, it is the cheapest material option. If you look at laminated glass it’s in a higher range and more or less comparable to polycarbonate but if you then want to further reduce costs in order to be competitive, you definitely have to save costs in the assembly stage by integrating functions into the injection molding step used to manufacture polycarbonate glazing.
Automotive IQ: That’s fascinating. Just going back to the spoiler you mentioned, was that actually a functional piece as opposed to a design cue? It also had the ability to produce some down force and affect the handling?
F.B.: Yes, and there’s more. There is a polycarbonate side window which already had a guiding profile in the side window for the movable window which was adjacent to it. So the guiding profile was injection molded into the fixed plastic glazing part, again to reduce assembly costs.
Automotive IQ: So you could potentially see the same drastic design changes that we’ve seen in headlights with a combination of polycarbonate, injection molding with LEDs, you could see that for the whole car?
F.B.: Definitely and, at the latest K Fair we, as a raw material producer, presented a complete tailgate including a backlight. Not only the glazing part but the complete tailgate was made out of one piece. You need some additional elements on the inside of the tailgate to get the stiffness because it’s a lightweight material and a metal frame has, of course, more stiffness. But it is possible and then you get a seamless tailgate. It was only a stimulus for designers, at car manufacturers to consider what is possible with polycarbonate. We just wanted to show it works. The fancy design is, of course, the responsibility of our customers.
Automotive IQ: And that starts to come later as people get more used to the material and used to working with it.
F.B.: And that’s also the problem. There are a lot of possibilities and we get a lot of interest but currently we have a limitation for all these fascinating ideas. We have regulations in place which mainly focus on glass and tests established for glass while from a safety standpoint the needs should, of course, be based on real use conditions.
Automotive IQ: Understandably, due to the age of the regulation…
F.B.: The regulation for safety glazing evolved in the past decades, and for example at the time the abrasion test was defined the question was more how can a certain glass surface quality be guaranteed and not so much what is the real wear a glazing part is facing in use. Nowadays considering other suitable glazing materials it is, of course, important to have abrasion tests which mimic the real situation on our roads. There are carwashes, the action of the wipers, maybe some sand in an airstream, or an ice scraper etc. That’s the issue, the real wear situation is quite complex and a single test is not able to cover all kinds of wear.
In general it´s normal when selecting tests for regulation to just use what was there and what was simple and gave the possibility to check if the glass is on the same level as it is normally. That’s not a problem for the new material. Of course, we passed all the mechanical tests easily because they consider what glass can deliver and glass is a brittle material. Polycarbonate glazing has a much higher impact resistance, so from that point it’s very easy for us to use what exists for glass because that’s a clear advantage of polycarbonate. But, on the other hand, glass is an inorganic, hard material and has a much higher surface hardness compared to coated polycarbonate and the problem there is that we cannot achieve the same level as glass because that’s the clear benefit of glass - it has a very high surface hardness. The question in this case is what type of wear resistance and what level is realistically needed? The level is probably somewhere in the range of glass, the type of wear should be as close as possible to use conditions. This is a question we are also discussing in the informal group. What is the real wear that a normal glazing part has to withstand? As we are considering windscreens, as mentioned, we are thinking about carwashes, about sand in the airstream or wiper resistance in order to mimic exactly what we have on the roads.