The Rise of Silicon Carbide (SiC) in Electric Vehicle Power Electronics
SiC in EV Power Electronics
Add bookmark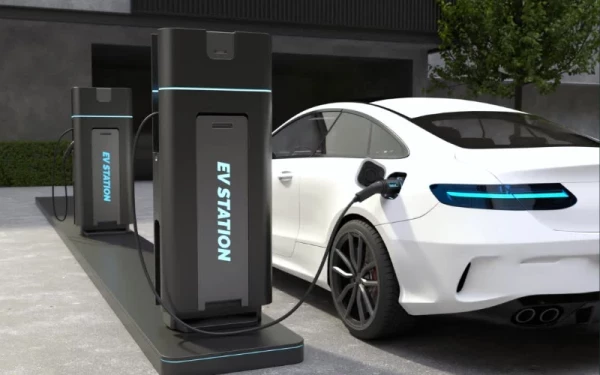
The Rise of Silicon Carbide (SiC) in Electric Vehicle Power Electronics
Written by Jack Shaw
Image source: Canva
Electric vehicles (EVs) are revolutionizing transportation, offering cleaner and more efficient alternatives to traditional internal combustion engine vehicles. Their power electronics systems are central to their performance and efficiency, which control the flow of electricity from the battery to the motor and other components. In recent years, a material known as silicon carbide (SiC) has emerged as a game-changer in EV power electronics, offering numerous advantages over traditional silicon-based solutions.
What Is SiC and What Role Does It Play in Emerging Electronics?
Silicon carbide is a compound semiconductor material composed of silicon and carbide atoms. Its unique properties make it highly attractive for use in power electronics applications. Compared to silicon, SiC offers higher breakdown voltage, faster switching speeds, lower on-resistance, and better thermal conductivity. These characteristics translate to more efficient and compact power electronic systems, making SiC an ideal choice for EVs.
SiC is revolutionizing how electricity is converted, controlled, and distributed. Traditionally, silicon has been the dominant material used in power electronic devices due to its abundance and relatively low cost. However, as these systems demand higher efficiency, greater power density, and improved reliability, SiC has emerged as a superior alternative.
The Advantages of SiC in EV Power Systems
The adoption of SiC in EV power systems represents a significant advancement in the quest for more efficient and sustainable transportation. SiC offers several advantages over traditional silicon-based solutions, making it an ideal choice for EV power electronics applications. Here are some of the key benefits.
Higher Efficiency
SiC devices exhibit lower switching losses and reduced conduction losses compared to silicon-based devices. This higher efficiency translates to less energy wastage during power conversion processes, resulting in increased driving range and improved overall energy utilization of electric vehicles.
Increased Power Density
SiC’s superior material properties, including higher breakdown voltage and thermal conductivity, enable the design of power electronics systems with higher densities. This means more energy can be delivered using smaller and lighter components, leading to compact and lightweight EV power systems. It also allows for integrating additional features and functionalities within the same space, contributing to overall vehicle design flexibility.
Enhanced Thermal Performance
SiC’s excellent thermal conductivity helps dissipate heat more effectively, reducing thermal resistance and allowing higher operating temperatures. This is particularly advantageous in EV power systems, where components often operate under demanding conditions. Improved thermal performance enhances the reliability and longevity of power electronics components, reducing the risk of thermal-induced failures and extending the life span of electric vehicles.
Improved Power Conversion Efficiency
SiC devices offer superior electrical properties, such as higher breakdown voltage and lower on-resistance, resulting in more efficient power conversion processes. This leads to reduced losses during energy conversion, optimizing electricity from the battery to the motor and other auxiliary systems in the vehicle. Higher power conversion efficiency enhances EV performance and contributes to lower operating costs and reduced environmental impact over the vehicle’s life cycle.
Greater Electron Mobility
One of the standout features of SiC compared to traditional silicon is its higher electron mobility, a measure of how quickly electrons can move through the material in response to the electric field. This property allows SiC-based devices to achieve faster switching speeds, leading to more efficient energy conversion and control in EV power systems.
Faster speed also reduces switching losses, minimizing energy wastage and improving system efficiency. Greater electron mobility lets SiC devices handle higher currents and voltages while maintaining stable performance. This makes them well-suited for demanding applications in electric vehicles, where reliability and performance are paramount.
Smaller Systems
SiC’s superior material properties, including higher breakdown voltage and thermal conductivity, enable designing smaller and lighter power electronic systems for electric vehicles. SiC devices let manufacturers achieve higher power densities, meaning more energy can be delivered using smaller and lighter components. This reduces the overall size and weight of the power electronic systems and allows for more compact vehicle designs.
Smaller and lighter power systems improve vehicle efficiency, range, and performance while enhancing EV owners’ driving experience. Additionally, the compact nature of SiC-based power electronics enables greater flexibility in vehicle design, facilitating innovative solutions for integrating power management systems into the overall vehicle architecture.
The Impact of SiC on EV Performance
Integrating SiC technology into EV power systems profoundly impacts the overall performance of these vehicles. SiC’s unique properties enable significant improvements in various aspects of operation, ranging from efficiency and range to acceleration and charging times.
Extended Range
The efficiency gains achieved directly translate to increased driving range. By optimizing power conversion and distribution, SiC technology allows EVs to travel longer distances on a single charge, addressing one of the key concerns of consumers regarding EV adoption. Motors and engines typically last at least 20 years, but the average EV battery only lasts 200,000 miles, which is less than two decades. Extended range enhances EVs' practicality and usability, reduces range anxiety, and accelerates the transition to electric mobility.
Enhanced Acceleration
SiC’s faster switching speeds enable quicker response times in power conversion and motor control systems, leading to improved acceleration performance in electric vehicles. Delivering power more efficiently and effectively results in smoother and more responsive acceleration, enhancing the driving experience. This increased acceleration capability contributes to the perception of EVs as high-performance and desirable alternatives to traditional internal combustion engine vehicles.
Faster Charging Times
The fast switching speeds of SiC devices enable higher switching frequencies in power converters, facilitating faster charging of EV batteries. Reducing charging times with SiC technology enhances the convenience and practicality of electric vehicle ownership, addressing one of the key concerns of consumers regarding adoption. Faster charging also contributes to EV charging infrastructure’s scalability, supporting the widespread deployment of electric vehicles.
The Durability and Longevity of SiC
SiC is well-known for its exceptional durability and longevity, making it an ideal choice for demanding applications such as EV power systems. The inherent properties contribute to its robustness and reliability, ensuring the longevity of EV electronics under harsh operating conditions. SiC exhibits excellent thermal stability and can withstand much higher temperatures than traditional silicon-based materials. This is crucial for EV power systems operating in environments with elevated temperatures due to energy dissipation and thermal cycling.
Its resistance to voltage surges ensures the robustness of EV power systems during regenerative braking and fast charging cycles, minimizing the likelihood of premature failures. SiC's chemical inertness protects it from corrosion and oxidation, ensuring long-term reliability even in harsh environments. Its radiation hardness makes it suitable for applications where exposure to ionizing radiation is a concern, ensuring consistent operation in space-constrained environments.
SiC devices demonstrate excellent long-term stability and reliability. They maintain performance levels throughout the vehicle’s life cycle and minimize the need for maintenance or replacement.
SiC components cost approximately three times more than traditional silicon parts with the same rating. The primary reason for this difference is the lower SiC supply compared to silicon. Overall, SiC technology ensures the long-term sustainability and viability of electric mobility, driving the widespread adoption of electric vehicles and shaping the future of transportation.
How Do Industries Adopt SiC?
Various industries, including automotive, aerospace, renewable energy, and telecommunications, are rapidly adopting SiC due to its superior performance and unique properties. SiC is revolutionizing EV power systems in the automotive sector, where its high efficiency, increased power density, and enhanced thermal performance are driving technology advancements.
Tesla was the first EV manufacturer to adopt SiC, and other companies followed suit. Manufacturers are increasingly incorporating SiC-based power electronics into EVs to improve energy use, extend driving range, and enhance performance. This adoption accelerates the transition toward electric mobility, offering consumers more efficient and sustainable transport options while reducing greenhouse gas emissions.
In the aerospace industry, SiC is used in avionics, propulsion systems, and power distribution systems to improve the reliability and durability of aircraft components. Its high-temperature tolerance, radiation resistance, and lightweight properties make it well-suited for aerospace applications, where performance and safety are paramount.
SiC also drives advancements in the renewable energy industry, specifically in solar inverters, wind turbine converters, and grid-tied storage systems. Its high efficiency and reliability make it an attractive choice for power conversion applications in green energy installations, where maximizing yield and minimizing maintenance costs are essential. Improving these technologies enables SiC to contribute to the widespread adoption of clean power sources.
Challenges in SiC Adoption
Despite its numerous advantages, SiC adoption faces several challenges. One is the cost associated with the manufacturing process. SiC devices are currently more expensive to produce than traditional silicon-based counterparts due to the fabrication complexity and lower economies of scale. As a result, the upfront cost can be a barrier to widespread adoption, particularly in price-sensitive markets such as consumer electronics and automotive applications.
Another challenge is the limited availability of SiC substrates and wafer sizes. While silicon wafers are widely available and come in large diameters, SiC substrates are less common and typically smaller, leading to higher production costs and limiting scalability. The shortage of large-size SiC wafers hampers mass production and impedes the commercialization of SiC technology in high-volume applications, such as EVs and renewable energy systems.
The Future Impact of SiC
The future of SiC is poised to be transformative across a wide range of industries, driven by ongoing advances in material science, manufacturing processes, and device technologies. SiC is expected to be pivotal in accelerating electrification in the automotive sector, enabling the development of next-generation EVs with improved performance and range.
SiC adoption in EV power electronics is projected to become more widespread as production scales up and costs decrease. This will lead to greater energy savings, reduced greenhouse gas emissions, and enhanced sustainability in the automotive industry.
SiC Is the Future
The rise of SiC represents a significant advancement in the field of electric mobility. Its superior performance characteristics, inducing higher efficiency, increased power density, and enhanced reliability, are driving innovation in EV power electronics. As the automotive industry transitions toward electrification, SiC is poised to play a pivotal role in shaping the future of electric vehicles, making them more efficient, reliable, and accessible than ever before.