Interview: Semi-Active Suspension Systems
Interview between Automotive IQ and Hans Gijrath, Global Product Management Lead at Tenneco
Add bookmark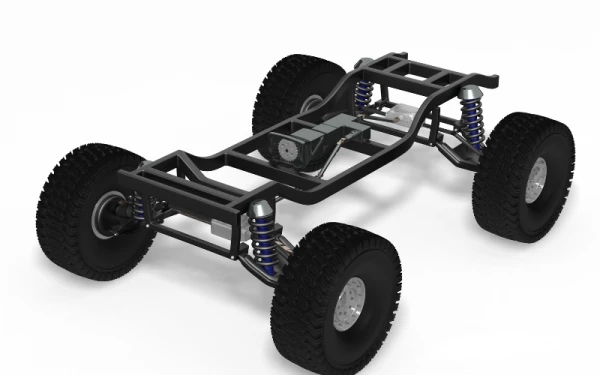
Semi-Active Suspension Systems: Interview with Hans Gijrath, Global Product Management Lead at Tenneco
In this insightful interview between Automotive IQ and Hans Gijrath, Global Product Management Lead at Tenneco, Hans provides invaluable insights into Tenneco's cutting-edge CVSA2/Kinetic suspension system, a technology known for its presence in McLaren hypercars. Throughout the discussion, Hans sheds light on the balance between comfort, agility, and stability in semi-active suspension systems, detailing Tenneco's innovative approaches to address evolving market trends and customer demands.
Hans presented at the Automotive Suspension Systems 2023 conference. It's here where he gave insights into Tenneco's so-called CVSA2/Kinetic suspension system, which is known mainly from the McLaren hypercars and is now being introduced by several other premium vehicle manufacturers for their SUV’s and/or sports cars. The presentation included a technical overview of the system, how it works, how it delivers key ride attributes to both SUVs and sport cars, as well as giving some insights into what applications have been launched in the market recently and which directions Tenneco is exploring to continue to innovate.
Q: Hans, how are you at Tenneco working towards designing semi-active suspension systems that keep heavy cars flat on the road during dynamic driving conditions such as cornering, braking, and accelerating?
Hans
The solutions we develop not only address how to keep cars flat on the road, (this is only one of several key attributes we need to manage), we do this rather well I should say. Ride comfort, agility, and brake performance are as much or even more important depending on the vehicle type. Our design of new (semi-)active products/solutions is driven by market trends and customer needs. Take for example the trend of battery electric vehicles; these vehicles have a significantly higher curb weight, so in order to bring the same comfort, handling, and agility compared to their ICE predecessors, more advanced suspension solutions are likely required to increase the level of vehicle dynamics control.
Another trend, software-defined vehicles, brings other opportunities for new suspension technologies, where software rather than hardware is bringing certain functions to the (semi-)active suspension system. The design and development process we apply is based on the so-called V-process, where vehicle requirements are cascaded to the suspension system and its components and the software to control the system. In the case of new technologies, several iterations of this cycle are required to come from a concept idea to a matured and validated solution that can then go into customer applications.
Q: How can semi-active suspension systems make a heavy SUV feel more agile, like a sports car?
Hans
Steering a heavy SUV around the corner or through a more winding road can be made easier for the driver if all chassis systems work well together; the steering maneuver is basically a sequence of events involving the steering system, the (semi-)active dampers, and roll control system. It starts, of course, by rotating the steering wheel to turn the wheels in the go-to direction, then the car starts to respond, and it will go into the expected direction. How well-controlled this happens depends on the first response of the shock absorbers.
If the shock absorbers can be controlled and set firmer when turning the steering wheel, the car will respond more directly, and the driver will also feel this positive feedback immediately. In case of a conventional suspension set-up, the driver may have to keep applying larger force on the steering wheel and/or make multiple corrections while going through the corners.
A semi-active roll control system, however, will keep the roll angle minimal and will maintain a much better steering response. The benefit of a system like Kinetic is, it maintains that high roll stiffness through the corner, also at very high lateral accelerations (tight corners) while also allowing single wheel inputs caused by road bumps to be nicely absorbed for the best comfort in all driving circumstances.
Q: How are you at Tenneco prioritising the enhancement of comfort, within the semi-active suspension systems in development?
Hans
Most customers want maximum comfort first. I think there are no truly uncomfortable cars made today, but in more premium segments people simply expect more. At Tenneco, we are addressing comfort in all our semi-active damping developments. These technologies use both passive damping valves and one or two solenoid valves to control the pressure difference over the damper piston, which translates into a damping force. We are making continuous development steps in both valve technologies. Very soon we will introduce 2 major steps in both the passive and solenoid valve technologies that we use. We have already demonstrated on test vehicles significant improvements combined with better tunability for OEMs to meet their specific needs.
Q: Furthermore, how can the industry effectively manage the conflict between agility, stability, and comfort?
Hans
These three attributes are a delicate balance, of which the sweet spot depends on the OEM’s DNA. With semi and fully-active systems this balance can be continuously optimised to different driving situations and road conditions. But in the end, every technology has a cost as well, so we will continue to see strong differentiation between vehicle segments and classes; low-cost cars may keep only conventional solutions whereas premium vehicles have more advanced solutions optionally. For top segments, we see these technologies as standard equipment most of the time.
Q: What factors have you considered to ensure the semi-active suspension system has excellent dynamics and agility?
Hans
There are multiple factors that must be taken into account: the suspension’s performance is very dependent on the vehicle (e.g. size, weight, wheelbase, height, and location of the centre of gravity), the sensors on the vehicle to detect the driving situation and the road conditions, then the electronic control unit in which the software (algorithm) continuously processes the sensor data to determine in real time what each suspension actuators should do and eventually the actuators themselves (i.e. dampers, hydraulic roll control unit). This is why our engineering teams work on all these aspects to be able to deliver our customers the best performance on comfort, stability, and agility. The interaction with the customer takes place during the entire development to capture the requirements, set up and test the system, and fine-tune it to make sure the perfect ride is achieved.
Q: What challenges have you faced in the development of semi-active suspension systems and what solutions were taken?
Hans
One big challenge in the automotive industry is cost. To be cost competitive, one needs to develop solutions that can be made in large enough quantities, use as much as possible of the same components, and still offer enough flexibility (tune-ability) to meet the different requirements of various customers. If we look at semi-active dampers, the active control valves (solenoids) are a high-cost contributor. So, we apply modular design methods to drive the standardisation of these control valves and still be able to efficiently manufacture enough tuning variants to cover each unique customer application.